MRP Summary (Modules)
Inventory Module
Part Numbers – 15 digits Alpha/Numeric
Last Purchase Price
Standard Price
Average Price (weighted
or simple)
3 Selling Prices
Lead Times (days,
weeks or months)
Serial Number Control
Minimum Stock Level
Review Level
Weight & Volume
Old Part Numbers
Alternative Parts
Drawing Issue Nos. & Effectivity Date
Dimensions (Flat
Pack & Rigid)
Warehouse Locations
Product Groups (and
Product Families)
Reservations Module
Single & Multi-Level Reservations
Singe Line Additions (SLA’s)
Explode Through Assemblies
Phantom Assemblies
Free Issue Support (Sub-Contract)
Free Stock / Exceptions Reporting
Ghost Kitting (acid
test) Reporting
Production Plan Gant charts
Overstocking & Imbalance Reporting
Issues Module
Planned Issues (Kit
& Part)
Unplanned Issues (Issues,
Credits, Adjustments and Stock Transfer)
FIFO or Full Traceability
Automatic Suggested Transfer (multi locations)
Perpetual Inventory (Part,
Product Group, Location)
WIP / JOB Costing
Outstanding WIP Valuation
Closed / Open Job Analysis
Cost Centres
Purchase Order Module
Supplier File
Delivery File
Postcode (PAF) integration
Maximum 200 items per order
Scheduling (as
far in the future as required)
4 decimal place pricing
Special Supplier Prices
Supplier Matrix Prices (Qty Break / Price)
Buying Cards (10
Suppliers, Preferred Supplier, Supplier Part References)
Automatic Re-Ordering Module (NEW or RE-SCHEDULE existing orders)
Approved Vendor Reporting
Supplier Document Profiles (print or email relevant documents)
Goods Received (single
or multiple GRN references)
Goods Inspection / Acceptance
Qty Advised / Qty Delivered / Qty Accepted
Discrepancy Reporting
Reject Control (including
Reject Notes & Debit Notes)
Supplier Performance
Outstanding Orders Analysis
Projected Purchase Analysis
Suggested Buying Reporting
Monthly Receipts Analysis (Turnover & Valuation)
Bill of Materials Module
Single Level & Multi-Level BOM’s
Change Control (Method
& Mod status)
Maximum of 99 levels
Unlimited parts per BOM
Sequence Level (for
PCB’s)
Lead Time Offset (for
Manufacturing & Purchase Modules)
Back Flushing options
Circuit Reference / Balloon Numbers
Mass Replace options
Product Structure (Serial
Number assembly)
Parts Lists (explosion)
Where used (implosion)
Assembly Valuation
Mass Re-Cost Assemblies (genuine or ghost)
Approved Vendor List
Gross Requirements Module
Support for Multiple Production Plans
Import existing Sales Order book
MRP-II / ERP calculations
Interactive Production Plan (user intervention)
Automatic Works Order Generation (MRP)
Activate / De-Activate Requirements
Gross Requirements Reporting
Sales Order Module
Customer File
Prospect File
Delivery Address File
Postcode (PAF) integration
Sales Enquiries / Quotations
Sales Orders (Genuine
& Pro-Forma)
Proforma / Export Orders
Mail Order Screen
Stock “allocation”
process per order (if required)
Real-time On-Hold, Credit Limit, Out/s Order
Balance (per customer)
Selling Prices
Customer Special Prices
Customer Type Special Prices
Pricing Matrix (Qty
Break / Discount)
Pricing Matrix (Qty
Break / Value)
Customer Product Group Discount
Customer Type Product Group Discount
Sales Price Lists
Customer Trade Discount
Parts Banding Matrix Grid
Customer Banding Matrix (Part
and/or Product Group)
Order Threshold Discount
Order Value Deals (Mix & Match)
Customer Price Lists
Settlement Discounts
Interactive Payment Terms
Credit Card Surcharges
Sales BOM (comprises
of lists)
Salesperson / Geographical Area / Promotion
Codes
Tariff / Commodity Codes
Cancellation / Returns Control
Sales Despatch / Invoicing
Credit Notes (manual
& automatic reversal of invoice)
Carrier Interface (Parcel
Force, FedEx, City Link, UPS, Home Delivery Network)
Intrastat / EC Sales module
Process Control
Planning / Method Sheets
Change Control (Method
& Mod status)
99 operations per sheet
Work / Load Centres
Manual & Machine (Setup
/ Runtime) times & costs
Overhead costs
Planning Sheet Costing (automatically linked to Sales Enquiry module)
Routing / Capacity Planning module
Scrap Analysis
Finite / Infinite Scheduling & Loading
Job Tracking / Performance
Time Recording / Analysis
Customer Progress Reporting
Work-To-Lists (Load
Centre, Customer or Part)
Serial Numbers
Serial numbers generated at Works Order,
Issues, Receipt or Despatch
BOM Serial Numbers (comprises
off assemblies)
BOX Serial Numbers (holding
multiple serial numbers in a larger box)
Dependant Serial Numbers
Automatic generation / printing of labels (environmental
specific)
Full Serial Number Tracking (through production & despatch)
Full production of Barcodes (all formats, EAN, CODE39 etc.)
Warehousing
Multi-Warehouses
Unlimited Bays / Levels
Drive-In Bays
Automatic Palletisation
Default BAY’s
Automatic Utilisation control
Automatic replenishment of Despatch Stores (loose
product)
FIFO Control
Mobile RF Handheld Barcode devices (forklift drivers)
Pre-Checking Sales Order Despatch
Sales Order Interaction (between picking staff & sales staff)
Global Warehouse Status Screen
Others
BS5750 / ISO9002 compliant
EDI Portal (passing
Orders, Invoices, Credits) to external systems, such as
Transalis, Amazon and Tesco
WEB Portal (batch
or real-time). Data can be sent “to
& from” websites, collecting orders, and providing information
for customer website and/or 3rd party websites
Remote Salesperson (Tablet/PDA)
support for Orders, Stock etc.
Financial Software Integration to products
such as Sage, Pegasus, Exchequer, Selima, Zisk. Most accounting
systems can be supported so long as they have import features
enabling TXT, CSV or XML formats.
Service System Module to support Sales Order
Processing. Warranty, Claims, Repairs, replacement (new
for old). Full job tracking and detailed historical records.
Automatic PDF reports
Automatic EXCEL integration
E-Mail Server (supporting
all Purchase Orders, Invoices, Credits, and Statements etc.)
sent direct to Suppliers / Customers
Quick Menu Access and Intuitive Menu design.
Pre-Defined Function Keys (user) to move around system quickly
Background Scheduler allowing automated
tasks, such as BACKUP, and regular reports to be run un-attended.
Automatic Stock notification tasks. System
can interactively inform users of Goods Received, Low Stock levels,
Back Flushing issues.
All pre-printed stationery documents catered
for (Kitting Lists, Material
Requisitions, Purchase Orders, GRN’s, Reject Notes, Sales
Quotations, Order Acknowledgements, Sales Picking Lists, Advice
Note, Invoice, Credit Note, Certificate of Conformity)
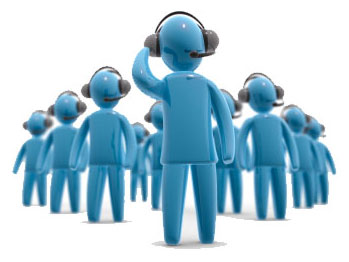